The Ultimate Guide to Cold Chain Temperature Monitoring
Ensuring the Safe and Efficient Monitoring of Temperature-Sensitive Food and Pharmaceuticals
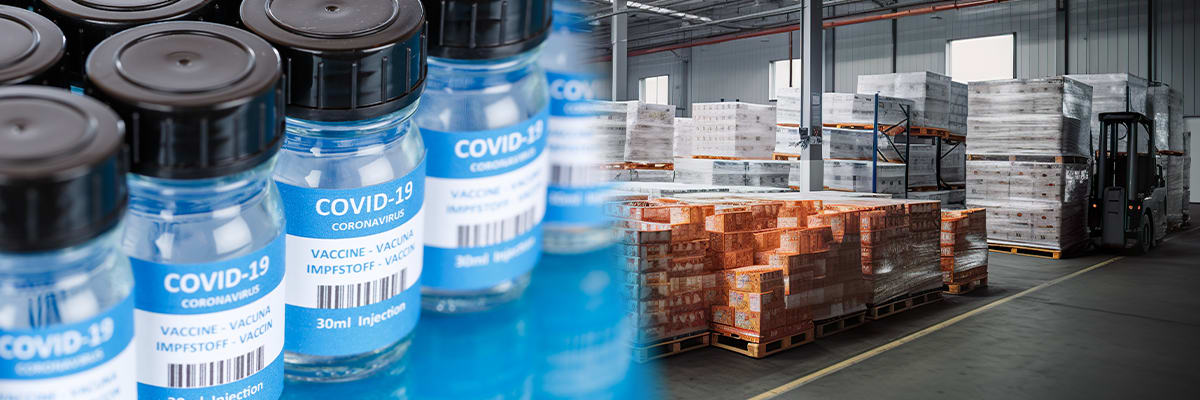
Whether you’re transporting perishable food items, pharmaceuticals, vaccines, or other temperature-sensitive products, precision temperature control throughout the supply chain is essential to preserve product integrity, safety, and regulatory compliance. This process of maintaining temperature standards from point of origin to the final destination is called the cold chain.
Cold chain temperature monitoring is the systematic temperature maintenance of refrigerated products throughout the entire supply chain, from production to storage, transportation, and distribution. It’s a critical part of the process, and it involves the use of temperature monitors, data collection systems, and analytics tools to ensure specified temperature conditions remain consistent at every phase.
To better understand how cold chain temperature monitoring works, let’s review the basics and how each element plays into the bigger picture to ensure products are delivered at the optimal temperature.
How Does Cold Chain Monitoring Work?
Cold chain monitoring relies on a network of temperature monitoring devices that travel with the cargo while in-transit or stored at a location. That means whether the product is in a shipping container, refrigerated truck, processing plant, cold storage facility, or even the freezer at your local supermarket, it has a cold chain monitoring device following it.
These sensors continuously monitor and record temperatures and other product conditions, transmitting data to a centralized system. The system then analyzes the data, compares it against predefined thresholds and regulations, and generates real-time alerts if deviations occur. This makes it possible to act quickly to rectify issues.
When Are Temperature Monitors Used?
Temperature monitors are used continuously from the point of production to storage at the final destination. Broadly, there are three stages of temperature monitoring: process monitoring, shipping and transportation, and storage.
Process Monitoring
In the context of cold chain management, process monitoring specifically focuses on temperature-related processes and variables. It requires the constant use of temperature monitors during manufacturing, processing, and handling to support quality control.
For example, some pharmaceuticals, such as insulin, require specific temperature conditions during processing and handling. Temperature monitors make it possible to identify deviations or abnormalities that could compromise the drugs’ effectiveness or consumer safety.
Shipping and Transportation
Accurate temperature monitoring is paramount when perishable goods are transported over long distances, especially across different climates. Frozen food items, such as seafood or ice cream, require constant low temperatures to maintain their texture and quality. Moreover, maintaining optimal temperatures enhances the product’s shelf life, whether it is frozen food or fresh produce.
Temperature monitors equipped with alarms can promptly alert logistics personnel of temperature deviations, enabling swift action to prevent product degradation in transit.
Storage
Temperature monitoring in storage is crucial to maintain product integrity. From warehouses and cold rooms to grocery store refrigerators and freezers, temperature monitors provide real-time data on temperature levels, ensuring compliance with storage requirements and safety regulations.
The Components of a Temperature Monitoring System
Temperature monitoring systems provide end-to-end visibility throughout the entire cold chain. The following components all play a role in safeguarding product quality and safety, from processing to purchase.
Temperature Sensors
Temperature sensors are the core component of any monitoring system. They come in various forms, including data loggers, wireless sensors, and probe thermometers. These sensors are strategically placed to accurately measure and record temperature levels at different points in the cold chain.
Environment Alarms and Door Alarms
Environmental alarms alert organizations to temperature fluctuations that occur while their product is in transit or storage. If the ambient temperature around the product is such that the product will not stay in its required temperature range, then a real-time monitoring device will sound the alarm so organizations can intervene and preserve their product in real time.
Door alarms are a subset of environmental alarms and play a crucial role in maintaining the integrity of temperature-controlled environments, especially in storage. These alarms alert personnel if doors are left open, allowing immediate corrective action to prevent temperature fluctuations.
Real-Time In-Transit Alerts
Real-time alerts are indispensable in temperature monitoring systems. These alerts promptly notify stakeholders, such as logistics managers or quality control teams, of any temperature deviations beyond pre-defined thresholds. By providing timely warnings, real-time alerts enable proactive interventions to minimize temperature excursions.
Dashboards and Reporting
Comprehensive dashboards and reporting tools allow stakeholders to visualize temperature data collected by the monitoring system. These user-friendly interfaces provide valuable insights into temperature trends, enabling informed decision-making and helping identify potential areas for process improvement.
Corrective Actions
Temperature monitoring systems facilitate the implementation of corrective actions. When temperature deviations occur, predefined protocols guide personnel on appropriate measures to restore ideal conditions.
Audit Trail
An audit trail is required for recordkeeping purposes, including traceability and compliance. It documents and tracks all temperature-related activities, creating a verifiable record of temperature monitoring and corrective actions taken. An audit trail is particularly critical in industries with stringent safety, recordkeeping, and regulatory standards, such as pharmaceuticals.
Data & Analytics
To further improve the cold chain process and support overall operating decisions, it’s important for teams to leverage data and analytics. Insights derived from shipping and transportation data can help cold chain teams make better decisions, which can positively impact the bottom line of an organization. However, ciphering through all of this information can be a daunting task. Organizations, such as Sensitech, has a dedicated team to each account to ensure that this data can be turned into actionable insights for your team.
What Sensors Are Used in Cold Chain Monitoring?
It’s common to use several types of temperature monitoring sensors throughout your cold chain. The type used will vary depending on the product and the stage of the supply chain (e.g., in transit or stationary). The main categories of temperature sensors are:
Data Loggers
Data loggers, or conventional temperature monitors, are one of the most widespread types of sensors. They’re used to record temperature readings at regular intervals during transportation or storage, providing a historical record of temperature conditions. These are often standalone devices that can be placed in the environment or attached to the product being monitored. They are commonly used for collecting temperature data over an extended period, and you can retrieve and analyze the recorded data.
Wireless Temperature Sensors
A wireless temperature sensor is a device that transmits real-time temperature data using wireless connectivity, such as Wi-Fi or Bluetooth. These sensors are often part of a larger, centralized monitoring system that enables personnel to instantaneously access real-time temperature information from disparate locations.
Probe Thermometers
Probe thermometers consist of a temperature sensor probe attached to a display unit. They allow users to insert the probe directly into a product or environment to obtain an accurate temperature reading. This can be useful for spot-checking the temperature of specific items (for instance, when products are unloaded at a distribution center) or in particular locations (such as in a grocery store display refrigerator or a specific section of a refrigerated warehouse).
Non-Digital Temperature Monitoring
Strip chart recorders, also called circular chart recorders, have been the standard for food temperature monitoring devices for over 100 years, though they can also be used in life sciences. These highly accurate sensors continuously record and display temperature data on a rotating paper chart, creating a visual representation of temperature fluctuations over time. They are often used during extended transit periods, and the tamper-proof, immutable record is valuable for quality control audits and regulatory purposes.
It’s important to note that large enterprises have thousands of temperature monitoring devices in use at any given moment. Often these devices, including digital data loggers and wireless sensors, can be reused multiple times. Many temperature monitoring manufacturers offer device takeback programs to refurbish and reuse digital monitoring devices, preventing them from ending up in landfills.
Why Cold Chain Temperature Monitoring Matters
Monitoring shipping temperatures has many benefits related to safety regulations, sustainability, brand protection, and waste reduction.
Regulations
Stringent regulations govern the transportation and storage of temperature-sensitive goods. Failure to comply can result in penalties, product recalls, and damage to a brand's reputation. Proper temperature monitoring ensures compliance with these regulations by providing an audit trail of temperature measurements at every stage of the cold chain.
Sustainability
A temperature monitor’s main function is to ensure products are stored and transported in optimal conditions. A secondary benefit of efficient temperature monitoring is the ability to minimize energy waste caused by excessive cooling or heating. Temperature monitoring optimizes cooling or heating systems by continuously adjusting temperature settings based on actual needs, minimizing energy consumption, and reducing carbon emissions.
Food/Medication Waste
Temperature monitoring plays a key role in another sustainability-related area: reducing product waste. Inaccurate temperature monitoring can lead to spoiled or compromised products, which must be discarded. By maintaining cold chain integrity, temperature monitoring prevents unnecessary product waste and financial loss. Additionally, by leveraging data and analytics collected from these monitoring systems, teams can understand how processes can be improved to preserve the quality of a product.
Industries Using Cold Chain Temperature Monitoring
Many industries are using the cold chain to transport materials, including automotive, aerospace, and manufacturing. Below are some examples of industries who rely on the cold chain to ensure product quality:
Pharmaceuticals
The pharmaceutical industry heavily relies on temperature monitoring to maintain the integrity and efficacy of certain vaccines. Cold chain monitoring ensures that medications are stored and transported within the required temperature range, protecting patient safety and compliance with regulatory standards.
Food
The food industry makes up over half of all perishable shipments in the world. For that reason, it’s no surprise they use temperature monitoring to preserve freshness, extend shelf life, and prevent bacterial growth. From farm to table, temperature control plays a vital role in keeping food safe for consumption. Restaurants, grocery stores, and food distributors rely on accurate monitoring systems to prevent spoilage and meet food safety requirements.
Temperature Monitoring Case Study
Sensitech has partnered with dozens of clients to address their specific cold chain temperature monitoring challenges. One notable case involved a California-based company shipping large amounts of dough to Asian markets. Quality complaints arose, and Sensitech conducted an end-to-end analysis. The study revealed that the quality issues were not related to ocean transport as the company suspected. Instead, it was determined that a third-party freezer in Korea was responsible for improper storage temperatures, causing the dough to spoil. After identifying and addressing the issue, Sensitech conducted a second study to verify the effectiveness of the corrected cold chain.
Selecting the Right Cold Chain Monitoring Partner
As the case study above illustrates, both size and expertise matter when it comes to selecting a cold chain monitoring partner. There are many vendors who supply temperature monitoring services, but not all are equipped to support scalability or international logistics.
Managing a global supply chain involves navigating complex regulatory frameworks, coordinating multiple locations, and ensuring seamless temperature control across borders. A reliable partner with experience in international logistics understands the intricacies involved in cross-border transportation, customs regulations, and handling temperature-sensitive products in different regions.
Scalability is also an important consideration, particularly for growing enterprises. As your business expands, you need a cold chain monitoring partner that can adapt and scale alongside your operations. This involves not only accommodating increased volume but also having the capability to integrate with your evolving processes and technologies. A partner with a robust infrastructure, advanced monitoring systems, and a proven track record of handling large-scale operations can provide the necessary support to accommodate your growth without compromising quality and efficiency.
Additionally, Sensitech has a team of experts dedicated to each customer account. These experts can help your team derive insights from your data analytics to ensure your company is making the best decisions possible when it comes to the cold chain process. Our years of experience gives you a competitive edge when it comes to shipping products across the cold chain.
Final Thoughts: Real-Time Cold Chain Visibility
Cold chain temperature monitoring plays a pivotal role in preserving the integrity and safety of temperature-sensitive goods. By employing a comprehensive monitoring system with temperature sensors, real-time alerts, and reporting capabilities, Sensitech can help you ensure regulatory compliance, reduce waste, and safeguard product quality.
However, cold chain monitoring is not a “one-and-done” solution. It is a process of continual improvements and slight tweaks to better optimize your cold chain and overall supply chain. It is important to routinely analyze weaknesses in the cold chain and what steps you can take to prevent temperature excursions and maximize product quality and shelf life.
Our real-time monitoring solutions simplify temperature monitoring through user-friendly features, including tablet-accessible applications. We make it possible to break free from clunky food safety solutions and achieve operational efficiency throughout your entire cold chain.
Interested in learning more about how Sensitech can deliver comprehensive cold chain visibility that scales with your business? Contact Us today.